4 Bed, 3 Bath, No Garage Door: The Unlikely Woes Holding Up Home Building
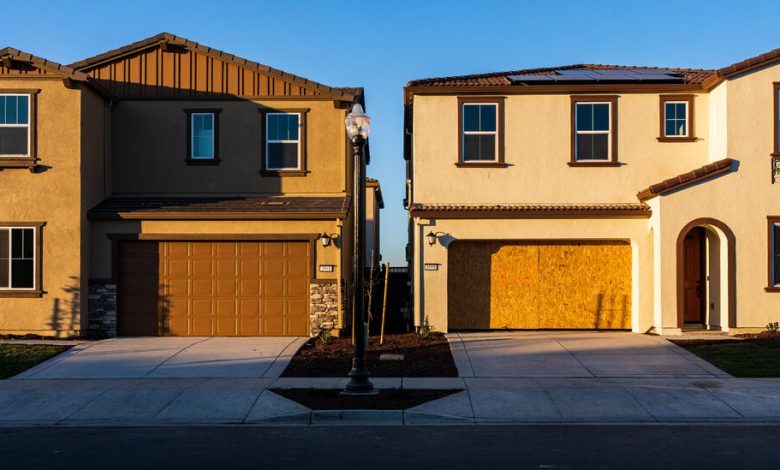
[ad_1]
Amid all this variety, a few problems have been acute lately. Many doors contain spray-foam insulation, which has been in short supply since the plants in Texas that manufacture its chemical components were disrupted in last year’s winter freeze. (If you make garage doors, you’re also competing for polyurethane or polyvinyl chloride with window frames, vinyl siding, caulking — and the aerospace, cruise ship and automotive industries.)
Many other garage door components are made from steel, which has also been in short supply. And even companies that manufacture the finished doors domestically typically source parts from China that have been snarled in global shipping.
In the Raleigh-Durham area, Wes Carroll’s custom home building company, Upright Builders, primarily constructs homes with three-car garages, split into a two-car side entry and one-car front entry. (“We build as few houses as possible with only a two-car garage, if that doesn’t sound crazy,” he said; local buyers expect three, especially on pricier homes.)
For that setup, he used to pay about $3,200. Now the cost is running about $6,000. He has one week to lock in the price. Then he’s waiting two to three months for delivery.
The unpredictability of rising costs and long lead times, the problem at the heart of home building today, has upended his business model. It used to be that you’d presell a home and then start construction, because home building is less risky when you know there’s a buyer. But all the risk is reversed right now.
“The way I’m putting it — and garage doors would fall into this category — we don’t know something is not going to be available until it’s not available,” he said.
And the latest word on the availability of Mr. Tomalak’s garage door, ordered on July 27 of last year?
“All we know,” he said, “is April or May.”
[ad_2]
Source link