Daimler Buses And OmniPlus Open 3D Printing Spare Parts Centre In Germany
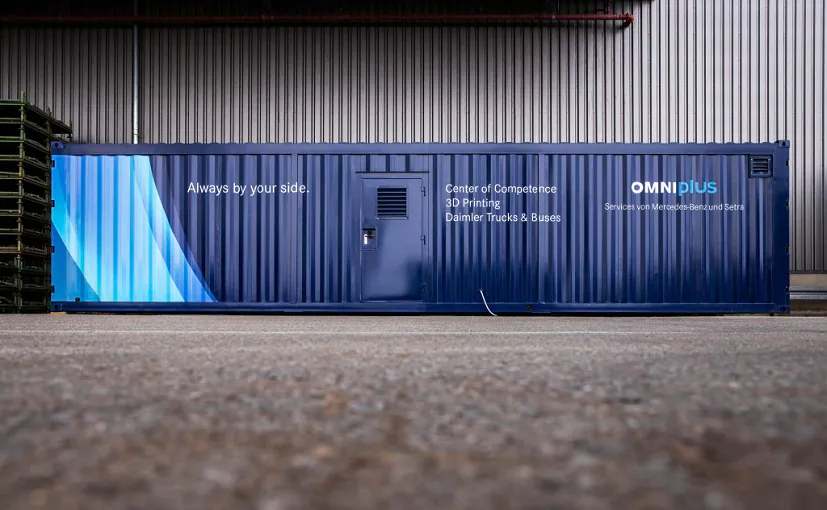
The mobile container is equipped with a top-quality industrial 3D printer which produces 3D printed products to the same quality as other genuine parts.
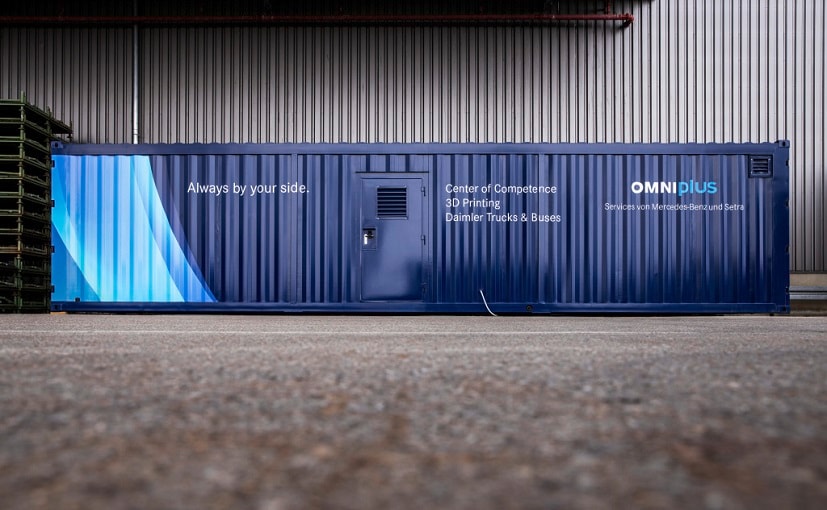
The container can be transported by truck to any location.
Daimler Buses and its service brand Omniplus have created a mobile printing centre for the decentralised production of 3D printed spare parts in order to be able to provide bus customers with spare parts more quickly. The “mini factory” in the form of a container includes all of the stations relevant to the production of spare parts using a 3D printer. The container can be transported by truck to any location. Once there, only electricity and an internet connection are required for its operation.
Also Read: Mercedes-Benz Concept EQT Unveiled

Daimler Buses is the first provider that can deliver series-production quality using a mobile solution.
The pilot container from Neu-Ulm will be in operation at the BusWorld Home (BWH) service centre in Hamburg. Daimler Buses is thus setting up a further production facility for 3D printed spare parts at the BWH Hamburg – in addition to the internal industrial 3D printing centre in parts production in Neu-Ulm.
The mobile container is equipped with a top-quality industrial 3D printer which produces 3D printed products to the same quality as other genuine parts. Therefore Daimler Buses is the first provider that can deliver series-production quality using a mobile solution. The 3D parts are additively manufactured using high-quality polyamide and meet the production standards for injection-moulding and deep drawn parts as stipulated by Daimler AG.
The 3D printing data is prepared at a CAD work station prior to the printing process. The required powder is prepared at a processing station where the printed spare part is also freed from residue powder in a final step. A blasting system and an air compressor are located in an adjacent room: the blasting system smooths the surface of the component parts for a perfect finish. Here, the printed spare parts can also be painted in a limited range of colours. The compressor provides the systems with compressed air. The container is also equipped with an industrial vacuum cleaner, an air filter and an air conditioning system.
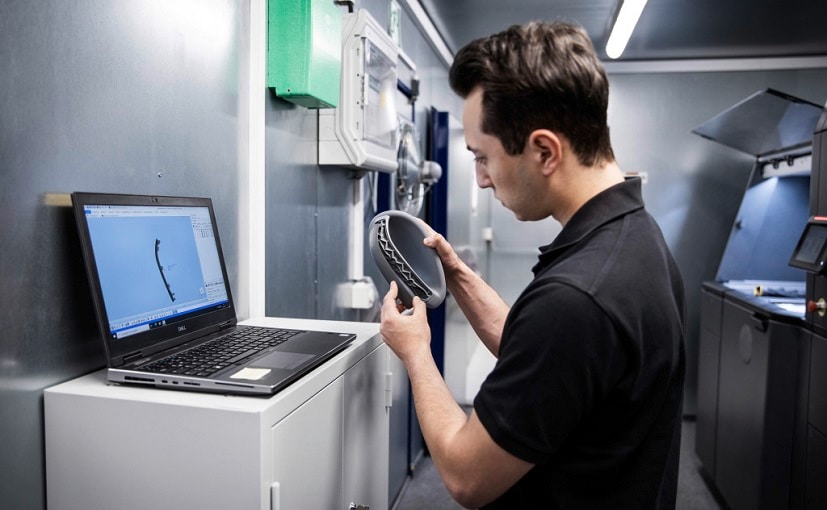
The 3D printing data is prepared at a CAD work station prior to the printing process.
0 Comments
Using 3D printing Daimler Buses can react fast and flexibly to urgent customer requirements, for example when customers order rarely required parts or have special requests. Instead of a wait of several weeks as for conventional spare parts, production and delivery of a 3D printed part takes only a few days. Just under 40,000 bus spare parts are already 3D printable today.
For the latest auto news and reviews, follow carandbike.com on Twitter, Facebook, and subscribe to our YouTube channel.