Wooden Buildings Reach for the Sky
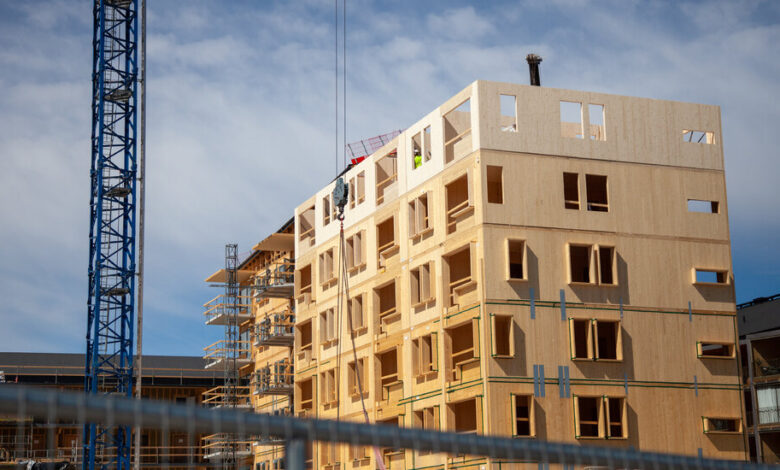
[ad_1]
VAXJO, Sweden — Stockholm and its suburbs are filled with construction cranes these days, reflecting a growing population combined with a housing shortage. But few of its developments are as extensive as Hagastaden, just to the north of central Stockholm where it meets the neighboring municipality of Solna.
Here, it looks as if an entirely new city is being built.
The 237-acre, or 96-hectare, development is a collection of housing, offices, institutions and public space projects conceived as a model of livability and sustainability, part of the Stockholm “Vision 2030” plan.
One section in particular is notable: two city blocks where a concrete foundation has been laid above a tangle of tunnels that funnel rail and road traffic to the north. It is an impressive feat of engineering, but the real significance is what is now rising from it, one of the largest apartment complexes built from timber in the world.
Cederhusen (or Cedar House) is the latest example of a growing practice of building big with what’s known as C.L.T., or cross-laminated timber.
It is a showcase for the industry of how far the technology has come.
Concrete is necessary for the foundation, but after that it is all wood, up to 13 stories at its highest point. The first block of two Cedar Houses is nearly complete and a second block is scheduled to start construction soon.
The tunnels below the development can only support so much weight. But because timber is about a fifth as heavy as concrete, the structure above the tunnels could be higher.
Using timber also has environmental benefits, the industry says.
“This is tech that we already have that can be used today, and it is a fast track to lowered emissions,” said Mathias Fridholm, the director of Svenskt Tra (“Swedish Wood”), an industry organization that promotes timber and wooden products. “But it’s not only the climate,’’ he added. ‘‘The whole building sector needs to be modernized and a good way of doing that is through a higher degree of industrialization.
“Wood is in many ways an excellent material for building in dense cities, because we can prefabricate all the elements in factories, instead of on-site.”
Mr. Fridholm said that prefabrication would speed construction and reduce disruptions such as constant truck traffic at the building site and road closures.
Because timber is lighter than concrete, floors can be added to existing buildings if there is a need for expansion, he said.
Timber accounts for roughly 20 percent of new multistory buildings in Sweden, but that figure is on the rise. That is happening in part because of companies like Folkhem, the real estate developer behind Cederhusen, which decided in 2012 to build exclusively in wood. The company is hoping projects like this, and around a dozen others in its portfolio, will help to tip the scales.
“This project is going to be really important because it’s a whole two blocks in inner Stockholm where you can choose to buy an apartment made out of timber,’’ said Anna Ervast Oberg, a project manager at Folkhem. ‘‘So it’s going to be a symbol of the possibilities and the techniques and industrial capability that we have.”
Over a plate of cinnamon buns in the small construction site offices at the Cederhusen site, Ms. Oberg said that just changing the structure of a building to wood from concrete would result in an immediate 50 percent reduction in emissions. She said that if you looked at the carbon emissions over the lifetime of a typical concrete building, roughly 70 percent would be just from the roughly two years that it is under construction.
“And then of course we can optimize the building further,” Ms. Oberg said. “We have other aspects like shorter construction time, less transport. Those make the numbers even better.’’
She added: ‘‘What we have to do now is to stop the emissions, very fast. This gives us a hint of where we should be focusing, where we can make the biggest difference.”
C.L.T.’s list of benefits is long. It is exceptionally strong and light. It is also breathable, meaning it holds heat but doesn’t need plastic layers to manage moisture, as concrete does. Concrete also requires sand, a finite resource that increasingly requires damaging procedures like drudging up the seabed, while managed forests can be replanted. As a bonus, a city built out of wood becomes an urban carbon storage facility.
Before 1995, this sort of thing wasn’t even allowed in Sweden, the result of rules established many years ago after fires ravaged primarily wooden cities across Europe. But adoption of European Union rules meant an end to the former two-story building limit.
The technology has been steadily developing since then, to the point that those in the industry say fire risk is on par with other materials. Recognizing that, building regulations are now function-based rather than material-based, which is to say that as long as developers can prove the building withstands critical threats, like fire, it doesn’t matter what it is made of.
As for height, the sky is theoretically the limit, according to Folkhem executives. But, they add, because timber is lighter, it needs added stabilization as it climbs. Above floors in the mid-teens buildings need added ballast, often in the form of concrete slabs.
As the technology progresses, that may change. The current record holder is an 18-story wooden building in Brumunddal, Norway. For scale, the building is just a little shorter than the Statue of Liberty.
All this works especially well in a place like Sweden which has well-managed forests, and plenty of them. Seventy percent of Sweden’s land is forest, double what it was 50 years ago.
One of the biggest apartment complex developments so far in Sweden, according to Folkhem, used around 211,000 cubic feet, or 5,975 cubic meters, of wood for the construction. That wood, the company said, was estimated to take around 20 minutes for the Swedish forests to regrow.
Building single family homes out of timber is, of course, nothing new. The majority of homes in Sweden are wooden, as in many places around the world. What is new is the push to build larger buildings, office structures or apartment blocks as well as infrastructure like bridges, using timber frames instead of concrete or steel. But although timber use is on the rise, concrete still dominates in the construction industry.
Tomas Nord, a senior lecturer at Linkoping University in Sweden, has spent years studying the timber industry. “It should be obvious that it’s superior to concrete,’’ he said of wood. ‘‘It’s efficient and fast. You can build exactly what the customer wants in the factory. It’s a renewable material. It’s strong, durable and light.”
Mr. Nord added: ‘‘The challenge is down to the industry structure, the value chains that we have built up over years. In any mature industry, you have an idea about how you have to operate to be profitable. Then if you say we have to change, there’s going to be resistance to that.”
Those in the timber industry say that they are optimistic. “We’ve gone from zero to 20 percent market share since 1994,’’ said Mr. Fridholm of Swedish Wood. ‘‘And it won’t take long to get to 30 percent.”
“The building industry is quite medieval,” Ms. Oberg said with a laugh. “But in the last few years it’s come to a tipping point. We see a lot of [timber] projects being built in Sweden. Other countries are doing the same.
‘‘It’s down to the climate change becoming so obvious,’’ she said. ‘‘But it also has been years lobbying, talking to politicians, working with their rules and regulations, building up competence among engineers and so on. And now we have a complete foundation, and we have reference projects, that show that it’s possible.”
Those projects range from simple seven-story apartment buildings to more striking examples. One company has plans to build timber windmills as tall as 500 feet, or 150 meters. A test version, standing at about 100 feet, was erected in 2020, and commercial production is expected to begin next year. The northern Swedish city of Skelleftea, another timber pioneer, has had an air traffic control tower built from wood since 2004.
The development isn’t happening only in Sweden, of course. New projects are going up around the world. Norway, in particular, has had a huge increase in wooden buildings.
The construction company Veidekke, based in Oslo, recently built two identical structures in Trondheim, Norway, one in timber and one in concrete. “What happened was they could make three more stories on the timber house and still save two million kroner [about $230,000] on the foundation work because it was easier to make,” Ms. Oberg said. “They also looked at the health of the construction workers and saw that the hours people were sick was much less in the timber project. Injuries were less, and construction time was shorter.”
The small city of Vaxjo, population 94,000, sits in the middle of the timberlands of Smaland Province, in southern Sweden. Among municipalities in Sweden, many see Vaxjo as the leader in timber construction, as wooden buildings have been at the center of the city’s strategy since the 1990s. The city government reached its target for at least 50 percent of all new buildings to be timber-framed as of last year, and the municipality says it is now working on new and more ambitious plans for building with wood.
When I visited Vaxjo last summer, Catharina Winberg offered to show me around the city. At the time Ms. Winberg was a local politician and chairwoman of the Vaxjo Kommun Foretag, which oversees much of the building as well as energy production in the city. (Earlier this year she left her position to to return to the private sector.)
What I saw was impressive. Whole sections of land outside of the city center have been designated as timber-only development areas. Around town were dozens of construction sites for timber apartment buildings, schools and more, many of them using energy-saving measures, in varying states of completion.
“We really believe in wood as a material — it’s circular, it’s renewable, and it’s healthy,’’ Ms. Winberg said. “And we have the resources close by, so we might as well take advantage of that.”
She added: “We started to work with this very early, and that has generated a lot of interest. People want to learn about our strategy and see what we’ve done. So we think it’s very important how we carry this on because there’s so many looking to us now.”
The latest flagship project in Vaxjo, now in the final stages of completion, is a glass-panelled timber structure at the center of town that houses the new main train station, City Hall and a small shopping center, with a hotel scheduled to be erected.
“I think people today are longing for things that are genuine,’’ Ms. Winberg said. ‘‘And this is a very genuine place to live, with genuine buildings. They’re made of the forest that we have around us.
‘‘We have a housing shortage in this country, but if we didn’t, you could just choose,’’ she said. ‘‘Do you want a concrete building or a wooden building. What do you choose? That’s quite easy I think. But we’re not quite there yet.”
The industry is getting closer as a new law in Sweden will require a comprehensive climate declaration for every new building starting in 2022. The calculation comprises the total impact from start to finish of construction, including materials and transportation. The thinking is that once everything is taken into account in a systematic way, the benefits of timber should become even more apparent.
And recent developments in the world may help the Swedish timber industry’s goals.
“One thing that I think people will start thinking more about now is you cannot take globalization for granted,” said Mr. Fridholm of the forest industry group.
“Today from Swedish sawmills, 70 percent is exported to other countries,’’ he said. ‘‘In the foreseeable future people will start thinking about what resources we have in Sweden that we maybe should use better than we do now. And the eyes will fall on the forest. What is the best way of utilizing that? We can build with wood and store the carbon there. We can support ourselves with that.”
[ad_2]
Source link